The top 3 NATA deficiencies in labs
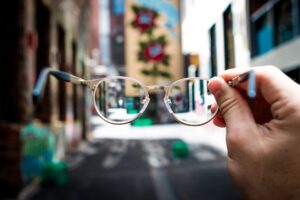
NATA deficiencies (aka conditions for accreditation) give you a clue on how you measure up. The question is, how common are those deficiencies?
You never really know how you compare with your peers, and it can be difficult to know what to focus on. Sure, there are those performance reviews, but are you being told the whole story?
This problem is magnified greatly when it comes to knowing how your organisation’s competitors are doing. What are they doing well? What are their weaknesses? How did they really perform at their last NATA assessment?
As consultants and mentors, we’ve visited a LOT of client’s labs over the years. And although each lab faces different challenges, we’ve found that there are NATA deficiencies that regularly crop up which can lead to some anxiety during audits or assessments.
At the recent Accreditation Matters conference, NATA helpfully identified the top 10 most common assessment deficiencies. In this article, we’re concentrating on the top 3 that both NATA and we at MAS find crop up on assessments time and time again.
If you have an audit or assessment coming up, you may want to investigate how you’re performing in these areas before the team arrives.
Issue 1: Competency
This is guaranteed to come up during an assessment. And while we’re sure all your staff are competent and know exactly what they’re doing, NATA won’t take your word for it!
In both ISO/IEC 17025 and ISO 15189, clause 6.2 covers personnel management. Labs are expected to have procedures and records in aspects ranging from the selection of staff, through to initial evaluation and ongoing monitoring of competence.
Many labs fall down with the description in their procedures for things like training, establishing competence criteria, and how staff are monitored for ongoing competence. Our advice is to keep it simple and describe, step by step, how your lab deals with these matters in your procedure.
One of the common causes we’ve found for this kind of deficiency is that labs don’t have these systems in place. We’ve written previously on good practice when it comes to training.
The next most common deficiency is doing what you say you do and having records to back this up. The common issues here are the complete or ad-hoc absence of records or the traceability to the activity where competence was demonstrated.
For the first issue of the absence of records, look carefully at your training records system. Is it super complicated with multiple places for recording the same training activity and competence determination? We’ve seen many labs with systems requiring the same information on training a staff member to be recorded on 3 separate forms! That’s a system fraught with danger.
When it comes to the traceability to the original activity, that’s a straightforward fix. One approach is to have copies of testing or calibration records attached to the training record, showing the results obtained by the trainee. Another way is to run an in-house proficiency test and keep those records attached to the training records. A simpler approach is to cross reference where those records will be found by noting the sample number(s), job number(s), or PT record in your training records.
A final word on competency: these competency procedures, criteria, and records need to include training, education, and experience for the various positions within the lab.
Issue 2: Equipment and Calibration
Another NATA deficiency that crops up from time to time is that labs don’t have all the equipment needed for the scope of accreditation. In those situations, the best approach is to develop your plan for acquiring these and be sure that this is recorded so you can show the NATA assessment team that you have considered any critical specifications for the equipment.
Once you have it…
Of course, obtaining the equipment is one thing. Calibrating and maintaining it is quite another. This is a BIG area of continued non-conformance.
The best advice is to plan a system that works. You could look at our previous article Keeping NATA happy about Calibrations for ideas.
You can periodically do a “health check”, asking simple questions like:
- What equipment does the method require?
- Do we have that equipment?
- Is it critical to the performance of the test or calibration?
- Does it need to be calibrated?
- What is the required traceability?
- Where are the calibration records and what is the calibration traceable to?
Another tip is to not only have a robust system to alert you to calibrations falling due, but also ensure you consider delays with calibration providers in factoring in the pre-calibration alert period. It’s a good idea to be in touch with the calibration providers well before to determine their lead times.
If you want to be sure that you’re on top of those pesky traceability requirements, check out our Complete Guide to Traceability.
Issue 3: Ensuring the validity of results
A NATA deficiency in this area can come from internal quality control and external quality assurance activities.
This section of the Standard specifies that your lab must have a procedure for monitoring the validity of its results. It also includes the required elements of the monitoring activities. Your lab must collect and analyse data from its monitoring activities and use these to evaluate (and potentially improve) its activities.
The common NATA deficiency in this section of the Standards relates to participation in an appropriate PT program and follow-up when poor results have been obtained.
When it comes to participating in PT, there are some broad requirements on frequency of participation. The NATA Proficiency Testing Policy sets out these requirements.
In a nutshell, your lab needs to participate in an external quality assurance activity at least once every two years for each major area of the scope of accreditation.
What do you do when there is no formal proficiency testing or external quality assurance program? That’s a very common problem faced by many labs.
If there is nothing available, you’ll need to explain why. You’ll also need to demonstrate what you’ve done to mitigate the risks of not participating in any activity with an external lab.
There is also some very valuable information on selecting a PT program developed by overarching laboratory organisations. Eurachem and Eurolab have great guidance on this area. Eurolab also has an interesting Position Paper to help with points of discussion with an accreditation body.
Do any of these issues sound familiar?
If not, congratulations! Your next assessment should be a breeze 😊
However, if you are facing problems with implementing any ISO/IEC 17025 clauses in your lab, we have some training that will help. Our upcoming courses in ISO 17025 Unpacked and Measurement Uncertainty Made Simple may be just the tonic you need! We’re offering these as virtual training experiences in August.
Our training is different. Naturally, we examine the clauses of the Standard and discuss their application in your lab.
When you attend an MAS course, there are lots of extra goodies on offer as a part of your registration. Things like tools and personalised follow-up.
We also understand that often the reason you want to attend training is because of a specific issue.
Perhaps there’s a clause you don’t understand or have difficulty implementing.
Or perhaps you thought you had it covered but at the last assessment, the lab was given a nonconformance.
So, we ask you to think about which clauses or aspects you need more information about; and which ones you’d like to discuss with someone outside your facility and get insights into its implementation.
Then we’ll ask you to send us those clauses and any specific questions before the course starts so we can drill down into those a bit more during the training.
So you’ll get exactly what you need to go back to the lab and implement it right away.
Sounds perfect, right? If you have a few people you’d like trained, call us and we can run an in-house session for you.
But perhaps you have an issue that doesn’t need a full day of training to address. That’s when our mentoring service can help.
To take advantage of these options, phone Maree (0411 540 709), or email info@masmangementsystems.com.au
Remember, you don’t have to do this alone!