Plan for success
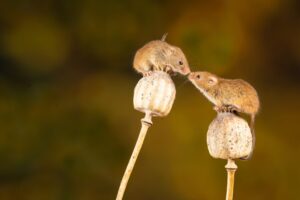
It’s been said that failing to plan is planning to fail. But sometimes we’re paralysed by the prospect of getting started and the time it takes to plan. Besides, there’s that other adage of “the best-laid plans of mice and men often go awry”. So you can only take these sayings with a grain of salt (hehehe!).
But, as one year ends and another begins, we’re often in the mindset of thinking about the future. Creating a plan for dealing with the future is the next step. You may already do some long-term planning, especially to achieve something really big.
What does it take to successfully plan for something? Well, read on and we’ll reveal some secrets!
Start with the end in mind
In business, setting goals is not really an optional extra. For many business owners, goals are vital to providing clear focus, motivating employees, and setting targets to work towards. Achievement of goals is a measure of success.
You should break your goals into short, medium, and long-term targets. There may be a relationship between each of these. Sometimes, the best way to see your way through to achieving a long-term goal is to break it down into more manageable, shorter-term goals.
Setting goals doesn’t have to be something you do on 1 January. But you do need to do it periodically. In the case of quality objectives or goals, the regular process of setting objectives, planning on how to achieve them, and reflecting on whether or not the objectives have been achieved is a requirement of all of the quality management system standards.
The reality of setting objectives is sometimes viewed as an airy-fairy exercise done just to satisfy the external auditors. That prompts the question, who are these objectives really serving if this is your reality?
So let’s talk about how to make good objectives that will serve your business.
What do you need to do?
This is where the various standards diverge in terms of what is required (sigh!).
ISO 9001 requires that quality objectives are
- consistent with the quality policy
- measurable
- formed with consideration to applicable requirements
- relevant to the conformity of products and services and to the enhancement of customer satisfaction
- monitored
- communicated
- updated as appropriate.
ISO 17025 does not call for objectives for quality.
Rather, it requires objectives for the “fulfilment of the purposes of the Standard” (they are found in the Introduction of the document).
These objectives must also address the competence, impartiality, and consistent operation of the laboratory.
ISO 15189 (2022) reflects the wording in ISO 17025, except that it does reference quality.
ISO 17020 requires the establishment of objectives for the “fulfilment of the Standard”.
So, if you happen to have an integrated management system that deals with multiple standards, you will need to take care when developing your quality objectives. But perhaps that’s just a matter of semantics.
Fortunately, most labs only need to deal with one standard.
Setting objectives that are meaningful and work
Much has been written about what makes a good objective. Acronyms like SMART (and SMARTER) abound in internet searches. However, setting a good objective requires a little more thought.
The starting point is to understand why you’re setting goals. Ideally, you do it because you want to, not because a standard or external auditor tells you that you have to. Remember, goals and objectives provide focus, motivate people, and set the target to work towards. But if you are setting an objective to tick a compliance box, then make sure it fits into the box.
However, when you set a goal, you communicate what is and isn’t important to others who help to achieve that goal. It’s necessary to understand the consequences of the path to achieving the objectives. Are you sacrificing other things that are important by not setting an objective?
Remember, there’s no rule about the number of objectives you can set.
Now you can adopt your favourite framework, like SMART, to set those objectives.
What’s SMART?
SMART is an acronym for ensuring the creation of good objectives.
S – specific
M – measurable
A – achievable
R – relevant
T – time-bound
An objective to test more samples is a little vague if you’re aiming to expand your lab. An objective of testing 50 % more samples in a new market that you already do a little work for, in the next six months, provides much more focus and direction.
A good quality objective might be something like: Receive no more than five customer complaints across the entire lab for the next 12 months.
That’s great to aim for, but if you never receive any more than three complaints each year over the past five years, is it meaningful? Of course, you’ll probably smash it, but does it lead to improvements in quality in your business?
Some ideas for making meaningful objectives:
- Use data from quality monitoring tools like trends in corrective actions, internal audits and identified risks
- Ask your staff what matters to them
- Ask your customers what they value in your service or one like it.
Finally, write the objectives down and communicate them to the people who will help your organisation achieve them.
What’s next?
Once you’ve set those meaningful objectives, then you have to plan how to achieve them. What resources do you need to devote to achieving the objective? Do you have to bring in additional staff or skill up existing staff? Do you need to refine your system to get better customer feedback? The options are endless, but remember, they are your plans and not those of the external auditor.
We suggest using the PDCA or PDSA cycle to help ensure success.
Plan-Do-Check (Study)-Act
The Plan-Do-Check-Act (PDCA) or Plan-Do-Study-Act (PDSA) cycle, also known as the Deming Cycle or Shewhart Cycle, is a systematic framework used for continuous improvement and quality management. Whilst it is normally used in processes such as dealing with problems (non-conformances) or improvement efforts, it is a useful model for any planning activity.
Plan
The first stage, “Plan,” involves identifying and analysing the problem or opportunity for improvement. It’s in this phase that organisations set specific goals, define the scope of the project, and develop a detailed plan to address the identified issues. This planning stage lays the foundation for subsequent actions and ensures that the activities and improvement efforts are aligned with organisational objectives.
Do
Following the planning stage, the second phase is “Do.” In this step, the planned improvements are implemented and executed.
Executing the plan is not a mindless exercise. It is crucial to carefully execute the plan and gather relevant data during the implementation to assess its effectiveness accurately.
The focus is on putting the planned changes into action, and this stage often involves testing and experimenting to understand how the improvements impact the overall organisation, process, or system. Progress reports can help in this stage.
Check / Study
The third stage is “Check,” or “Study”, where organisations evaluate the results of the implemented changes.
This involves comparing actual performance against the goals set during the planning phase. Did you achieve the goal?
The secret is to analyse data to determine whether the objectives were met and to identify any variances or unexpected outcomes.
This phase provides valuable insights into the effectiveness of the changes and helps organisations make informed decisions about whether to continue, modify, or abandon the implemented improvements. That’s why it’s sometimes referred to as the “Study” phase, where we also look for what can be learned from the data and so that we get sustained improvements in the organisation.
Act
The final stage of the PDCA/ PDSA cycle is “Act.”
Based on the findings from the checking phase, organisations take corrective actions and make adjustments to further enhance the organisation, process, or system. This phase completes one iteration of the PDCA cycle and sets the stage for continuous improvement. The lessons learned from the previous cycle are applied to refine the process, and the cycle repeats as organisations strive for ongoing excellence and optimisation.
In essence, the PDCA/ PDSA cycle serves as a dynamic and iterative framework that encourages a culture of continuous improvement within organisations, promoting adaptability and responsiveness to changing circumstances.
It provides a structured approach to problem-solving and decision-making, ultimately contributing to the sustained success of an organisation in a constantly evolving environment.
The Final Word
We know that business owners and managers don’t have a lot of time on their hands for deep thinking. There’s ALWAYS something to do!
If you’d like to discuss any of the issues we’ve raised in this article including training or business support, email info@masmanagementsystems.com.au or contact Maree (0411 540 709) to set up a confidential discussion.
Remember, you don’t have to do this alone!